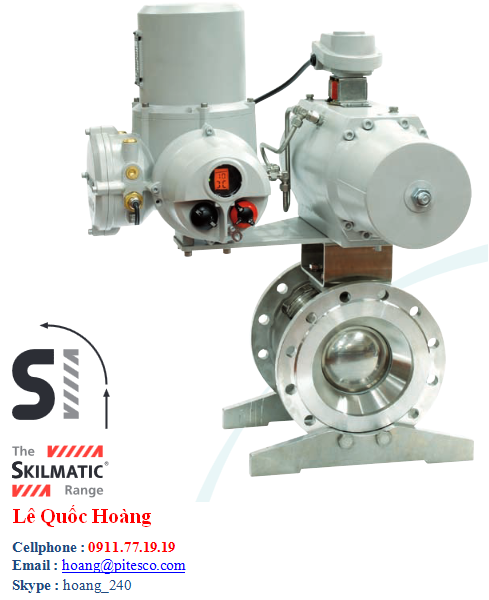
SI-2.1-Q Rotork Việt Nam
Hãng sản xuất: Rotork
SI-2.1-Q Rotork Việt Nam
“Intelligent” Electro-hydraulic Quarter-turn Valve ActuatorThe SI-Q are compact and robust electrically operated failsafe spring-return, quarter-turn actuators for two-position, ESD or modulating applications. They feature the Rotork double-seal system with separate termination and cable gland compartments, are suitable for all types of quarter-turn valves and are supplied with a mounting flange to ISO 5211. The quarter-turn range is divided into two groups: SI-1Q with end torque ranging from 65 to 480 Nm (575 to 4,248 lbf-in), and SI-2Q / SI-2.1Q with end torque ranging from 380 to 4,400 Nm (3,360 to 39,000 lbf-in). SI-2.1Q actuators are watertight and dustight to IP67 / NEMA 6 with the option of IP68 and are also available certified explosionproof for hazardous area gas group IIB and IIC applications.Consisting of a self-contained electro-hydraulic control module and scotch yoke spring-return drive, the actuators combine the simplicity of electrical operation with the precision of hydraulic control and the reliability of spring-powered fail-safe action. The spring-return mechanism provides the most reliable means of positioning a valve to the safe condition and can be provided as failsafe close, open, or last position on loss of power or signal failure. They are available with either a clockwise or anticlockwise spring stroke. For modulating control applications, the control module provides a pulsed hydraulic signal to accurately position the spring-opposed cylinder, resulting in accurate positioning with a resolution better than 0.2°. The actuators can be configured to accept analogue, digital, or network card input and can be programmed with the Rotork infrared setting too. A wide range of functions can be set with the tool: zero and span limits, deadband, hysteresis, slow band, and partial stroke position are easily adjusted. Optional internal fieldbus communication boards are available for Rotork Pakscan, DeviceNet, Profibus, Foundation Fieldbus and Modbus digital control systems.Lockable local controls are provided as standard and, for safety critical applications, the local selection can be overridden –proper actuator configuration required. Electro-mechanical end-of-stroke limit switches are also offered for safety critical applications.A manual override gearbox is available on all sizes
Features•Self-contained electrically operated with internal low-pressure electro-hydraulic control module.•Spring-return for failsafe open, close or lock-in-last position.•Single-phase, three-phase and 24 VDC power supply options.•Non-intrusive commissioning and configuration via our hand-held infrared setting tool. •Local LCD display provides position and internal pressure indication as well as and fault diagnostics.•Local controls include a lockable Local / Stop / Remote selector and an Open / Close switch.•Modulating control via 4-20 mA input/output with a resolution < 0.2°. •Digital control with ESD and partial stroke capabilities.•Output relays for monitoring, fault alarms and open/close limits.•Optional fieldbus communications via all common protocols.•Watertight and explosionproof. •Double-sealed control module with separate terminal and cable gland compartments.•Spring-return speeds: single, dual or ESD combination valve options.
CertificationATEX- II 2 G EEx de* IIB T4 (Tamb -50 to +60 °C)ATEX- II 2 G EEx de* IIC T4 (Tamb -20 to +60 °C) EN60079-0, EN60079-1, EN60079-7, EN13463-1INMETRO: BR-Ex de IIB T4 (Tamb -20 to +60 °C)INMETRO: BR-Ex de IIC T4 (Tamb -40 to +60 °C)Note: Certification temperatures are not operating temperatures.Setting Tool: ATEX, EEx ia IIc T4 (intrinsically safe) FM, INT SAFE Class I, Div 1 Groups A, B, C, D.CSA, Ex ia, INT SAFE, Class I, Div 1 Groups A, B, C, D.INMETRO, BR-Ex ia IIC T4 (intrinsically safe) Supplied only with INMETRO approved actuators.Safety Integrity:Designed to SIL 3.Enclosure:Watertight to IP67 / NEMA 6, double-sealed protection with separate cable gland and termination compartments. Optional to IP68 (7 meters / 72 hours). Consult factory for alternative depth / pressures. SI-2Q100 to Q130 & ESD option is only available to IP67.MaterialsControl Module: Aluminium. Piping: 316 Stainless steel (hard piped).Paint Finish: 2-pack epoxy silver grey (150 microns thick).Actuator – Q60 TO 80.Actuator Housing:Anodised aluminium. Piston:Aluminium. Driving Shaft:Zinc plated steel.Actuator – Q110 TO 112. Actuator Housing:Carbon steel. Drive Shaft:Carbon steel.MechanicalOperating Temperature:See table 8.Torque/ Speed:See table 1.Stroke:0°± 2.5% to 90° ± 2.5%.Weight:See dimensional detail (page 2 & 3).Failure Mode: Fail safe in the direction of the spring or fail in last position.Action: Spring-return clockwise or anti-clockwise.Hydraulic Fluid: See table 8.Max. WorkingPressure:12 bar (175 psi).Manual Override:Optional gearbox (on SI-2Q60 to Q80) or hydraulic hand pump (on SI-2Q60 to Q130).Internal Pressure Transmitter: Displayed as a percentage of maximum working pressure.Mounting:Valve stem vertical or horizontals (see table 9).ElectricalElectricalSupply:1-phase 115 or 230 VAC, 3-phase 380 to 480 VAC or 24 VDC. Supply Tolerance:Supply voltage ± 10 %. Frequency 50/60 Hz ± 5 %.Power Consumption:Power direction: 1-phase 320VA, 3-phase 240 VA, 24 VDC 225VA maximum.Motor Protection:Thermal cutouts, insulation class F.Cable Entries: Power module has a minimum of two spare entries (see table 7) plus two plugged M20 cable entries. See drawing SMW-SI-010 for options. Switchbox spare entry will be plugged: ATEX = M20, FM/CSA = ½”NPT.PositionFeedback:1 kΩ conductive plastic
Electrical continuedRemote Digital Inputs:Open, close, maintain, ESD and partial stroke. 20 to 60 VAC/DC standard or 60 to120 VAC optional. Consult factory for other voltages. 5 mA minimum duration 300 ms. DC inputs must be +ve switched.Limit Switches:Two adjustable electro-mechanical SPDT volt-free switches. Rating 5 A minimum at 230 VAC (see table 10).Non-Intrusive Setting:Sealed control module with infrared settingfrom the Rotork Setting Tool. All values are held within EEPROM to maintain settings within the memory on power failure. The actuator does not use a battery back up.Display:LCD display for viewing of the valve position, internal pressure and diagnostics screen. LEDs are provided to indicate limits and intermediate state in the remote mode. ControlControl Options:Remote digital (open, close, maintain), emergency shutdown and partial stroke; or analogue modulating (input 4-20 mA or 0-10 VDC).Resolution: <0.2% of full scale.Repeatability: <0.2%.Duty Rating: 90%.Output:4-20 or 20-4 mA, powered internally by an isolated 24 VDC supply or external customer supply.FunctionSettings:Deadband and hysteresis adjustable 0-99%, Partial stroke adjustable 0-99%, interrupt timer and ESD action.Interrupt Timer:To slow the rate of travel. Pulse ON and OFF duration selectable from 100 ms to 99 sec. Timer does not operate with loss of power.Local Controls:Lockable Local/Stop/Remote selector switch and local Open/Closed switch. Alarm and Limit Relays:Volt-free normally open or normally closed contacts rated 5 mA to 5 A 120/230 VDC, 30 VDC. Alarm Monitor relay: De-energised on loss of mains power; hardware, local controls or position sensor fault; or EEPROM error. Optional signal inverted to de-energise monitor relay for low power applications.Alarm Fault Relay: Energised on position, pressure sensor fault, over pressure mid-travel (torque) under pressure, stalled, incorrect direction, loss of control signal and hydraulic control module fault. Also on unsuccessful partial stroke and alarm monitor faults described above.Limit Relays: Two latching relays to indicate when the actuator is at the open or closed limit set within the software. Fieldbus CommunicationOptions:Internally mounted.Pakscan:Rotork fieldbus system forremote control and status indication over a fault tolerant two-wire serial link. Modbus: Single and dual communication highways. RS485 Modbus protocol RTU.Profibus DP: Fully compatibility with EN 50170. FoundationAn IEC 61158-2 compliant interface Fieldbus:module allows connection to a Foundation network.DeviceNet:ODVA certified DeviceNet interface with full status data feedback, digital and analogue control.Consult RFS regarding resolution on all fieldbus cards for for modulating applications.Rotork reserves the right to change specifications without notice